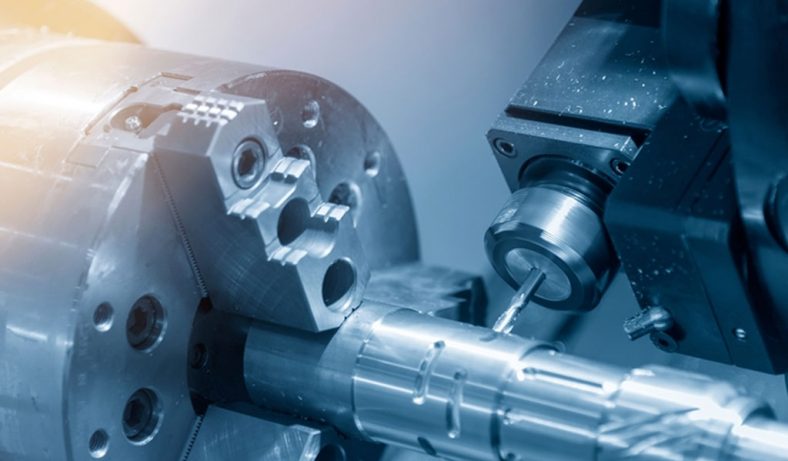
Wir verfügen über ein engagiertes Forschungs- und Entwicklungsteam, das stets maßgeschneiderte Fertigungslösungen für Sie entwickelt. Tatsächlich verfügen wir als eingetragenes High-Tech-Unternehmen mittlerweile über einundzwanzig Gebrauchspatente für die Herstellung, weitere acht befinden sich in der Entwicklung. Diese Patente belegen unser Engagement für ständige Verbesserung und Kundenzufriedenheit.
Da wir jedes Jahr mehr als tausend neue Produkte herstellen, sind dies nur einige Beispiele dafür, wie unsere Maschinisten und Ingenieure zusammenarbeiten, um Werkzeuge und Vorrichtungen zu entwickeln, die die Qualität verbessern und Ihnen gleichzeitig Zeit und Geld sparen.
Eine pneumatische Haltevorrichtung
Das starre Halten dünnwandiger Teile in einem Schraubstock oder einer Vorrichtung für die CNC-Bearbeitung kann schwierig sein, da die Teile viel Druck und Drehmoment aushalten müssen, es aber möglicherweise nur wenig Halt gibt. Manchmal werden solche Teile vorübergehend auf eine Opferträgerplatte geklebt, was zeitaufwändig und ineffizient ist. Gibt es einen besseren und schnelleren Weg?
Hierbei handelt es sich um eine pneumatische Haltevorrichtung. Damit es funktioniert, wurde ein Luftschlauch an einen Anschluss in der Bodenplatte angeschlossen. Unter hohem Vakuumdruck wurde Luft durch eine Reihe komplizierter Kanäle in der gesamten Mittelplatte gezogen. Dies trug dazu bei, den Unterdruck gleichmäßig zu verteilen.
Die obere Platte zeigt das Außenprofil des dort montierten Werkstücks, in diesem Beispiel eine aus Aluminium gefertigte Handyhülle. Vakuumvorrichtungen sind keine Seltenheit, aber wir geben uns besondere Mühe, solche Vorrichtungen auch für nur wenige Teile herzustellen, um sicherzustellen, dass jedes Teil perfekt herauskommt.
Eine automatische Indexiervorrichtung
Bei zylindrischen Teilen müssen häufig Merkmale rund um den Umfang in präzisen Winkeln bearbeitet werden, beispielsweise bei Rotoren und Zahnrädern. Manchmal kann dies durch manuell eingesetzte Positionierungsstifte erfolgen, die in einer Grundplatte montiert sind. Diese helfen dabei, die Drehung des Werkstücks zu kontrollieren, müssen aber auch bei jedem Bearbeitungsvorgang entfernt und neu eingestellt werden, was langsam und umständlich ist.
Stattdessen haben wir eine automatische Indexiervorrichtung wie diese hergestellt. Es verwendet pneumatische Antriebe, um das Werkstück um eine präzise Gradzahl zu drehen, um die verschiedenen Flächen präzise zu bearbeiten.
Die Zusammenstellung dieser gesamten Baugruppe erforderte ein wenig Ingenieursarbeit, aber das Schöne daran ist, dass sie in Zukunft für andere Projekte verwendet werden kann. Wir müssen lediglich die Indexierungsblöcke neu positionieren, um unterschiedliche Rotationsgrade um die zu bearbeitende Kreisform zu unterstützen.
Eine Vorrichtung für sphärische Teile
In diesem Beispiel standen wir vor der Herausforderung, die mehrseitigen Platten eines Fußballs zu fräsen. Der Trick hierbei besteht darin, sicherzustellen, dass die fertigen Elemente einheitlich sind und keine Überlappungen, Lücken oder Fehlausrichtungen rund um die Kugel aufweisen. Aber wie kann man das Teil rund um 360° sicher halten, ohne die Ausrichtung zu verlieren?
Wir haben diese Vorrichtung entwickelt, um die Kugel beim Fräsen in der richtigen Ausrichtung zu halten. Wir haben dies in einem zweistufigen Prozess durchgeführt. Zunächst wurde ein Rohmaterialrohling teilweise zu einer Halbkugel ausgearbeitet, wobei die Basis der Kugel jedoch auf einem sechseckigen Positionierungsblock montiert war.
Dieser Block hielt die Kugel, während die obere Hälfte auf unserer 5-Achsen-CNC-Maschine gefräst wurde. Die 5-Achsen-Fräse war hier ideal, da sie komplexe Drehungen um mehrere Achsen ausführen kann, ohne dass die Kugel neu positioniert werden muss, was möglicherweise zu einer Fehlausrichtung führen könnte.
Sobald die Oberseite des Balls fertig war, wurde er umgedreht, die Haltevorrichtung abgeschnitten und der Rest des Balls fertiggestellt. Da der Positionierungsblock zur Orientierung nicht mehr zur Verfügung stand, wurden Passstifte verwendet, um die Kugel entsprechend der Position der vorherigen Fünfecke zu indexieren.
Automatische Tiefziehkernentfernung
Diese Form wurde für die Herstellung eines langen, dünnwandigen hohlen Kunststoffrohrs entwickelt. Beim Kunststoffspritzgießen werden die meisten Teile normalerweise mithilfe von Auswerferstiften aus ihren Hohlräumen ausgeworfen. Aber Stecknadeln hinterlassen immer Spuren, und in diesem Fall war das für den Kunden nicht akzeptabel. Außerdem funktionieren Auswerferstifte bei Tiefziehteilen mit langen Kernen nicht so gut. Gibt es einen besseren Weg?
Wir haben eine maßgeschneiderte, automatische Abisolierform gebaut. Hierbei wurden die Kern- und Hohlraumplatten gegen vier starke Federn zusammengepresst und vorübergehend durch Verriegelungsplatten gehalten. Diese Baugruppe wurde dann in die Spritzgießmaschine montiert, wonach die Sicherungsplatten entfernt wurden.
Nach dem Öffnen der Form drücken die Federn die Formplatten auseinander. An diesem Punkt aktiviert der Hydraulikkolben den Schieber, der wiederum den Einsatz zurückzieht. Anschließend wird das Kunststoffrohr durch eine Abstreifplatte vom Einsatz abgedrängt, das fertige Teil fällt frei und der Zyklus kann wiederholt werden. Keine Auswerferstifte und keine Zeugenmarkierungen.
Wir bieten Ihnen Lösungen für alle Ihre Fertigungsanforderungen
Dies sind nur einige Beispiele für den zusätzlichen Aufwand, den wir unternehmen, um sicherzustellen, dass Ihre Teile so schnell wie möglich und mit den höchsten Standards an Effizienz und Wiederholbarkeit hergestellt werden. Unser Forschungs- und Entwicklungsteam wird weiterhin innovative und patentierte Lösungen entwickeln, um Ihren speziellen Anforderungen gerecht zu werden. Erfahren Sie mehr darüber, wie unsere CNC-Bearbeitungs- und Kunststoffspritzgussdienste Ihr nächstes Projekt unterstützen können, oder laden Sie Ihre CAD-Dateien für ein kostenloses Angebot hoch.