Das Vakuumgießen von Polyurethan ist eine großartige Möglichkeit, schnell Prototypen herzustellen. Zum Gießen weicher Silikonkautschukformen werden feste Urmodelle verwendet. Mit diesen Formen lassen sich bis zu zwanzig Kopien des Originals mit hervorragender Oberflächengüte und nur minimaler Investition in Rohmaterialien herstellen.
Es gibt noch einen weiteren Vorteil des Vakuumgießens, von dem viele Menschen nichts wissen. Wir sind eines der wenigen Unternehmen, das auch das Umspritzen von Vakuumgussteilen anbietet, was bedeutet, dass zwei oder mehr verschiedene Harze in separaten Schritten zu einem einzigen fertigen Stück kombiniert werden. Hier erfahren Sie, wie es funktioniert und warum es möglicherweise eine weitere großartige Option für Ihre Produktentwicklungsanforderungen ist.
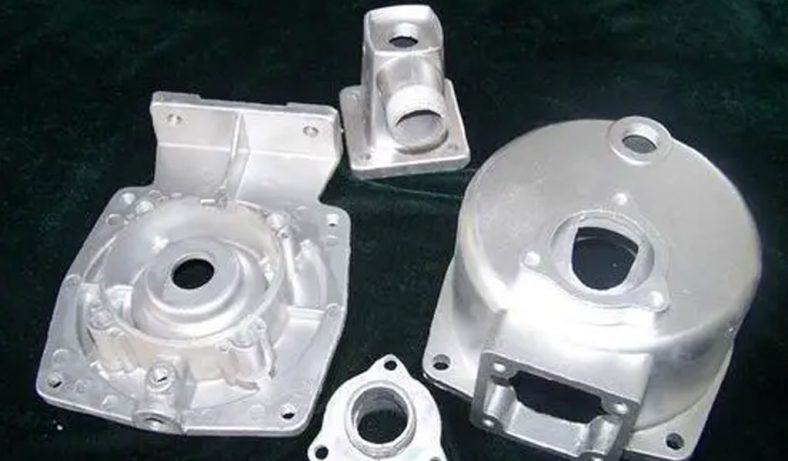
Was ist der Zweck des Umspritzens?
Durch das Umspritzen entstehen fertige Produkte, die über mehrere Texturen, Härten und mechanische Eigenschaften verfügen, die in einem einzigen einheitlichen Teil integriert sind.
Dies ist bei Serienproduktionen von Kunststoffspritzgussteilen nicht ungewöhnlich, beispielsweise zur Herstellung weicher, strukturierter Griffe an Elektrowerkzeuggriffen. Aber nur wenige wissen, dass dies auch mit Polyurethan-Vakuumguss möglich ist, wenn man die richtige Methode anwendet.
Muster erstellen
Beim herkömmlichen Vakuumgießen ist für jedes Formteil ein Urmodell erforderlich. Für das Umspritzen sind mindestens zwei separate Muster und zwei separate Formen erforderlich, die sich geringfügig voneinander unterscheiden.
Das erste Muster ist eine Nachbildung dessen, wie das fertige Teil aussehen soll.
Das zweite Muster wird ähnlich sein, abzüglich des Bereichs, der überformt werden soll.
Die Erstellung dieser beiden Muster wird mit moderner CAD-Software erheblich vereinfacht, wodurch es einfach ist, Abschnitte des 3D-Modells dort, wo die Umspritzung erfolgen soll, digital zu löschen. Diese überarbeiteten Modelle können problemlos an einen 3D-Drucker gesendet werden, um die Teilmuster zu erstellen.
Casting-Kopien
Sobald Sie diese beiden Muster haben, werden sie wie gewohnt mit Silikonformen umgossen. Das Silikon wird gegossen, man lässt es aushärten, dann werden die Formen geöffnet und die Muster entnommen, wodurch zwei leere Hohlräume entstehen.
Die kleinere der beiden Formen, die Teilform, wird zum Gießen eines Kopieteils verwendet. Da dieser Teil das Fundament des Baus bildet, muss er aus dem härteren, steiferen Harzmaterial gegossen werden. In diesem Beispiel wird das Hartplastikgehäuse mit einer weichen, strukturierten Tastatur und einem Rahmen umspritzt, der den zentralen Anzeigemonitor umgibt.
Nach dem Aushärten wird die Form erneut geöffnet und das kleinere, teilweise fertige Gussexemplar entnommen. Diese Kopie wird in den Hohlraum der größeren Form in Originalgröße eingelegt.
Da der Hohlraum in der zweiten Form größer ist, entsteht beim Einlegen der teilweise fertigen Kopie in diese Form ein kleiner Spalt zwischen ihr und den Wänden des Hohlraums. Diese Lücke stellt den Bereich dar, der überspritzt werden soll.
Überformen
In der größeren Form fertigen wir „Zuleitungen“, die zum Umspritzbereich, zur Blende und zum Tastenfeld führen. Nachdem das Teil in die Form gelegt wurde, wird die Form versiegelt und das Sekundärharz, das weichere Elastomer, wird in den Hohlraum gegossen, um die Zuleitungen zu füllen.
Diese Form wird in die Vakuumkammer gestellt und erhitzt, bis sie vollständig ausgehärtet ist. Dadurch entsteht eine dauerhafte Verbindung zwischen den beiden Materialien. Dieser Vorgang kann theoretisch mit einer unbegrenzten Anzahl von Überformharzen durchgeführt werden. In der Praxis empfehlen wir nicht mehr als zwei Harze, um Komplexität zu vermeiden und die Wiederverwendung der weichen Silikonformen einzuschränken.
Dies ist nur ein weiterer Weg, mit dem wir versuchen, den besten Rapid-Prototyping-Service in der Branche anzubieten. Wenn Sie der Meinung sind, dass Vakuumguss das Richtige für Ihr nächstes Projekt sein könnte, laden Sie noch heute Ihre CAD-Zeichnungen für ein kostenloses Angebot hoch.